Nanocrystalline and amorphous ribbons are two materials that possess unique properties and find application in various fields. Both these ribbons are used in different industries due to their distinct characteristics, and understanding the difference between them is essential for utilizing their potential effectively.
Nanocrystalline ribbon is a material with a distinctive structure composed of tiny crystalline grains. These grains are typically smaller than 100 nanometers in size, giving the material its name. The small grain size provides several advantages, such as higher magnetic permeability, reduced power loss, and enhanced thermal stability. These properties make nanocrystalline ribbon a highly efficient material for use in transformers, inductors, and magnetic cores.
The enhanced magnetic properties of nanocrystalline ribbons allow for higher efficiency and power density in transformers. This results in reduced energy losses during power transmission and distribution, leading to energy conservation and cost savings. The improved thermal stability of nanocrystalline ribbons allows them to withstand higher temperatures without significant degradation, making them ideal for applications in harsh industrial environments.
Amorphous ribbon, on the other hand, is a non-crystalline material with a disordered atomic structure. Unlike nanocrystalline ribbons, amorphous ribbons do not have identifiable grain boundaries but rather possess a homogeneous atomic arrangement. This unique structure provides amorphous ribbons with excellent soft magnetic properties, such as low coercivity, high saturation magnetization, and low core loss.
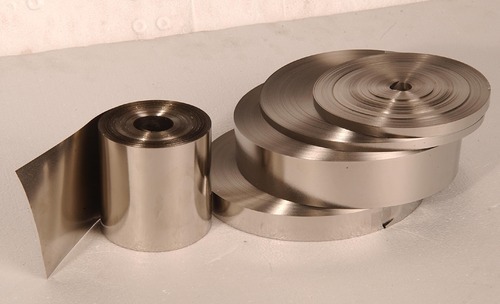
Amorphous ribbon finds widespread application in the manufacturing of high-energy transformers, magnetic sensors, and electromagnetic interference (EMI) shields. Due to their low core loss, amorphous ribbons are highly efficient in converting electrical energy into magnetic energy, making them suitable for high-frequency power applications. The low coercivity of amorphous ribbons allows for easy magnetization and demagnetization, thereby reducing energy losses during operation.
One of the significant differences between nanocrystalline and amorphous ribbons lies in their manufacturing process. Nanocrystalline ribbons are produced by rapid solidification of a molten alloy, followed by controlled annealing to induce the desired crystalline structure. On the other hand, amorphous ribbons are formed by rapidly cooling the molten alloy at rates of millions of degrees per second to prevent the formation of crystalline grains.
Both nanocrystalline and amorphous ribbons have their unique niche in the market, catering to different industrial needs. The choice between these materials depends on the specific requirements of the application in terms of magnetic performance, temperature stability, core loss, and cost-effectiveness. The inherent characteristics of nanocrystalline and amorphous ribbons make them crucial components in power electronics, renewable energy systems, electric vehicles, and various other modern technologies.
In conclusion, nanocrystalline ribbon and amorphous ribbon offer distinct advantages in different industrial applications. Nanocrystalline ribbons provide improved magnetic permeability and thermal stability, making them ideal for use in transformers and magnetic cores. Amorphous ribbons, on the other hand, possess excellent soft magnetic properties and low core loss, making them suitable for applications in high-energy transformers and EMI shields. Understanding the differences between nanocrystalline and amorphous ribbons enables engineers and manufacturers to select the most appropriate material for their specific needs, ensuring optimal performance and efficiency in their products.
Post time: Nov-02-2023